WIG-Schweißen
von Alurohren (AlMgSi0,5, 30 /5 mm)
Die
Knickrohre, ca. 15 m je Seite, bestehen aus ca. 2 x 6 m Rohren, die in
den notwendigen Bereichen in Bug und Heck auf ca. 3,5 m Länge gebogen
wurden (siehe Rohrbiegen). Als Reste einzuschweißen
blieben so an die 3 m, als gerade Stücke. Pro Knickrohr ergaben sich
am Heck in der Achse eine und im Mittelbereich je zwei Schweißstellen,
am Bug werden die Rohre am Bugbogen angeschweißt. Die gebogenen
Teile wurden an die schon aufgestellten Spanten und Schotte mit Draht
befestigt. Die Stationen der Spanten und Schotte lt. Plan entlang der
Rohre aufgetragen, stimmen sehr gut mit der "Natur" überein.
Die Biegung im Bereich der einzusetzenden Teile war sehr gering.
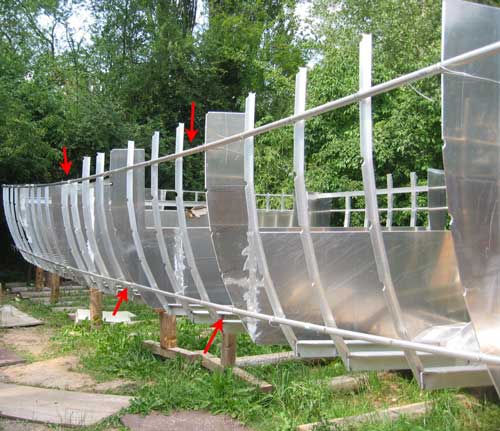
Die
Schweißstellen der Rohre.
Es mußte ein ca. 3 m langes Stück eingesetzt werden.
Hier war das Schweißen noch einfach, da die weiteren Rohre noch
fehlten.
Eine
Trockenübung mit dem MIG-Push-Pull-Brenner war nicht sehr ermutigend.
Die Naht erfolgreich um das Rohr zu führen schien, für mich,
unmöglich, da die bereits vorhandenen Spante und die anderen Rohre
keinen Bewegungsspielraum für einen so großen Brenner zu ließen.
Also war die Idee es mit WIG zu versuchen. Brenner ist leichter beweglicher
und alles schön langsam.
Die
Rohre abgenommen von den Spanten, zu verbinden, hätte zwar die Möglichkeit
ergeben in jeweils bester Lage zu schweißen, allerdings wäre
ein ca. 15 m langes Rohr mit je einem "Horn" von 1,5 m an jedem
Ende zu drehen. Und das immer bei halbfertiger oder nur gehefteter Naht.
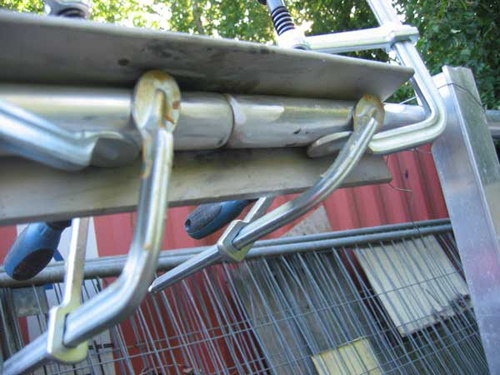
Die
Rohre wurden ca. 45 Grad an beiden Seiten des Stoßes gefast,
um eine V-Naht zu erreichen, mit einem VA-Winkel verklemmt.

Den
VA-Winkel wollte ich noch durch 4 Platten ergänzen,
um das Drehen ohne Schleifen der Naht zu ermöglichen. Hierzu später
Die
ersten Versuche zu schweißen waren zwar am Ende ok, aber es dauerte
viel zu lange und eine beträchtliche Menge an Schweißstab floß
in die Naht, sowie einige Male Ausschleifen von mangelhaften Nahtstücken.
Alles eigentlich grauenhaft, im Vergleich zu nachher, nachdem ich fachmännischen
Rat von zwei Mitgliedern aus zwei Internetforen (Werkzeugforum/Schweissen
und MetalBoatSociety-Forum)
bekommen hatte.
Die
Schwierigkeitsgrade setzten sich zusammen aus :
- schlechte
Position für den Schweißer, zwischen vorhandenen Rohren,
Spanten und Schotten,
überkopf schweißen, alle Schweißpositionen, rund um
das Rohr
- Rohre
zu schweißen scheint so oder so keine leichte Aufgabe zu sein,
war mir aber nicht bekannt...
-
die Führung des Schweißstabes gleich schwierig wie die des
Brenners. Der Stab darf auch nicht andere Teile des Gerippes berühren,
da er sich sonst festschweißt, Strom ist überall...
-
praktisch meine erste, ernsthafte WIG-Naht.
Autogenerfahrung mit Rohren hatte ich und es sollte eigentlich der gleiche
Ablauf sein, eben nicht ganz...
-
Durchschweißen ist notwendig
- Das
Setzen der Parameter am Gerät war mir noch nicht geläufig.
Die Werte aus der Literatur waren nicht so recht hilfreich.
Die Wahl von Elektrode und Detailparametern so noch schwierig.
Die
Hinweise der beiden Forumsmitglieder führten dann zu folgenden Lösungspunkten:
- Für
die Handhabung des Brenners waren feine Handschuhe notwendig, um den
kleinen Schalter am Brenner in allen Positionen betätigen zu können.
Hab da einige im Laden durchprobiert, um ein engsitzendes und nicht
verschnittenes Paar zu finden.
- Die
Handhabung mußte gegenüber dem MIG-Schweißen etwas
geduldiger erfolgen.
- Die
Schweißerhaltung muß durch Schemel, durch Unterlagen mit
Höhe zum Liegen für's Überkopfschweißen, Abstützung
der Hände für eine ruhige Führung von Brenner und Stab
(ohne sich zu verbrennen) an anderen Teilen in der Nachbarschaft der
Schweißnaht.
- Wenn
die Elektrode versehentlich ins Schweißbad eintaucht, schweißen
sofort unterbrechen, unbedingt die Elektrode um das verunreinigte Stück
durch abschlagen mit einem Hammer kürzen. Sonst wird der Lichtbogen
instabil/breit/unkontrolliert und verunreinigt das Bad.
- Die
Elektrode zu einer runden und glänzenden Spitze abschmelzen (ist
eine Funktion am Gerät).
- Verwendung
der Möglichkeit die Stromstärke auf Knopdruck am Brenner abzusenken.
Die Hauptstromstärke läßt das Material schmelzen, die
abgesenkte gerade nicht. So kann man das Schweißbad zwischen Schmelze
und knapper Erstarrung steuern. Diese Phase ermöglicht es, den
Schweißstab und sich selbst nachzuplazieren und den unnötigen
Aufbau von Stabmaterial in der Naht zu vermeiden. Da man ja ständig
die Position ändern muß, sehr hilfreich. Dies war für
mich der wesentliche Unterschied zum Autogenschweißen, dort kann
man diese "Absenkung" durch vorübergehende Entfernung
der Flamme erreichen. Hier würde der Lichtbogen abreißen
und keine Gasabdeckung mehr stattfinden. Dieser Wechsel erfolgt sehr
oft im Sekundentakt, quasi manuelles Pulsen...
- geschweißt
wurde mit Wechselstrom (AC), mit 4-Takt Betrieb - geringe Anfangs- (40A),
steigend auf Hauptstromstärke (150), nach Bedarf Absenken (65 A)
durch Rückzug des Schalters am Brenner und am Ende eine Absenkung
auf 40 A mit Nachströmen des Gases. um Krater zu vermeiden. Gasvolumen
ca, 8 ltr/min. Elektrode Cer-Oxid (grau) 2,4 mm und Schweißstab
2,4 mm, 5183.
Die Wellenbalance wurde auf neutral gestellt (beide Phasen gleich lang),
die Wellenform blieb auf Sinus.
- Den
Lichtbogen möglichst unter 6 mm halten, war schwierig genug und
natürlich nicht eintauchen.
- Den
Schweißstab nur ins flüssige Schweißbad führen,
nicht mit Lichtbogen abschmelzen.
- Falls
einiges w.o. angeführt schief geht, wird die Naht "schaumig"
mit schwarzem Oxid durchsetzt und damit nicht die erwünschte Festigkeit
erreicht. Und, so würden beim Verschweißen der Platten zwischen
den Rohren mit MIG, diese Stellen aufbrechen / verbrennen.
- Da
diese Nähte runtergeschliffen werden müssen und damit nicht
in dieser Endform bleiben, ist ein bißchen Matrial hier nicht
so tragisch...
- Die
Rohre müssen unbedingt offen sein. Sollten sich Abschnitte zusetzen,
besteht die Gefahr, daß der Druck das aktuell flüssige Schweißbad
kurz vorm Schließen des Rohres nach innen zieht. Werde in allen
Abschnitten kleine Löcher vom Bootsinneren bohren. Profis warten
bis sich das Schweißbad zurückzieht, schieben den Stab nach
und schließen diese Naht mit abgesenktem Strom. (Wohl eher nichts
für mich ...)
Die
Schweißfolge im Sinne einer Uhr :
VA-Winkel
festklemmen und Schweißen überkopf von ca. 5 bis7 Uhr. VA-Winkel
abnehmen und weiterschweißen von 5 bis 2 und von 7 bis 10 Uhr. Dann
wurde abgeschliffen, der VA-Winkel von unten fixiert und leicht angezogen.
Unmittelbar nach dem Nahtrest zwischen 10 bis 2 diesen Winkel mit den
Schraubzwingen vorsichtig festgezogen. Damit bekommt man evtl. Verzug
wieder zurück auf das Soll.
Die
abgebildete Schweißnaht, die erste nach Veränderung der o.a.
Umstände, hatte ich nur mit der ersten VA-Winkel-Fixierung durchgeführt.
Einen leichten Verzug konnte ich durch weiteres Anwärmen mit langem
Lichbogen an der Außenseite des "leichten Knickes" wieder
rausarbeiten. Werde sehen ob ich die Handhabung des Winkels bei den weiteren
25 Nähten so oder so verwenden werde. Die Veränderung des VA-Winkels
w.o beschrieben, lasse ich vorerst.

War
ein Erfolgserlebnis, etwas überhöht, wird aber geschliffen.
Eine
Bemerkung noch: für Profis ist dies natürlich alles nichts Neues.
Wollte aber im Sinne eines Amateurbootbauers die Hilfestellung durch Profis
und mein Erfolgserlebnis mitteilen. Hatte zwar auch alles schon irgendwie
gelesen oder gehört, war aber nicht in der Lage in der Aufregung
des ersten WIG-Schweißens alles so stimmig hinzubekommen.
©
2004 aluriver-crew |